General Overview
A low-pressure steam plant uses input energy (e.g., fuel, gas, or biomass) to generate steam in a boiler, which is then distributed throughout a facility or group of facilities for heating. Low pressure steam plants are generally operated at 15 psig or less (steam temperature below ~250 F). Low pressure steam can be used directly as a heating medium and distributed to the terminal equipment, or it can be used indirectly by being piped to heat exchangers to heat water to use at terminal equipment and/or domestic hot water (DHW) systems. A low pressure steam plant and associated systems are shown in Figure 1. A steam plant consists of a steam boiler, steam distribution system, condensate recovery system, blowdown system and economizer.
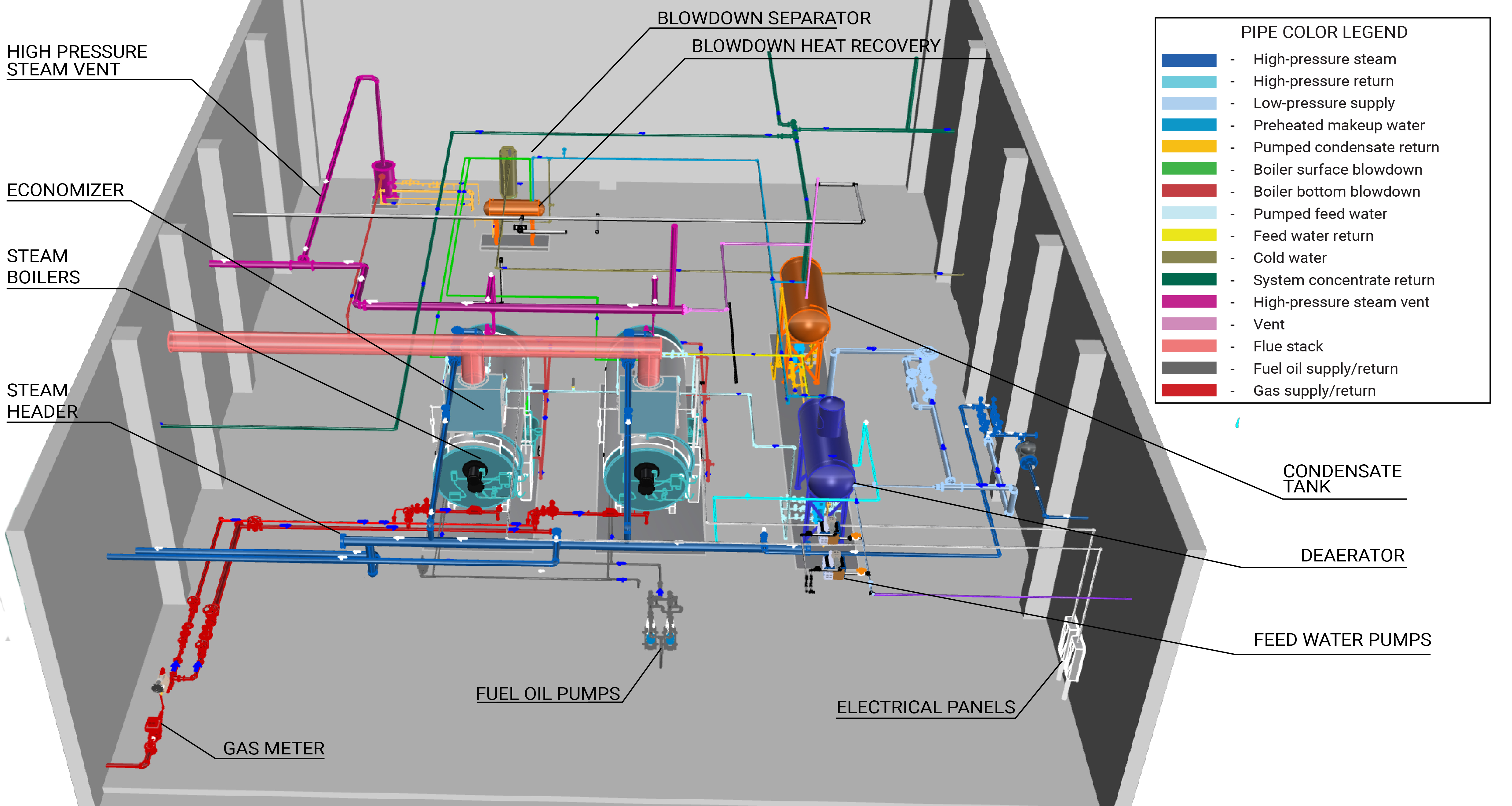
Systems
Steam Boiler
A steam boiler system is the largest energy-consuming system in the steam plant. A steam boiler generates steam by transferring heat from the combustion gases in the combustion chamber to the water. The steam produced is then transported out to the facility to meet the heating loads. Learn More
Steam Distribution System
A low-pressure steam distribution system supplies the steam to the facility or facilities. Steam distribution systems are generally closed-loop, where the steam condensate is returned to the steam boiler to be re-heated (see Condensate Recovery System below). The steam distribution system contains various valves and steam traps to regulate heating and manage condensate throughout a building. Learn More
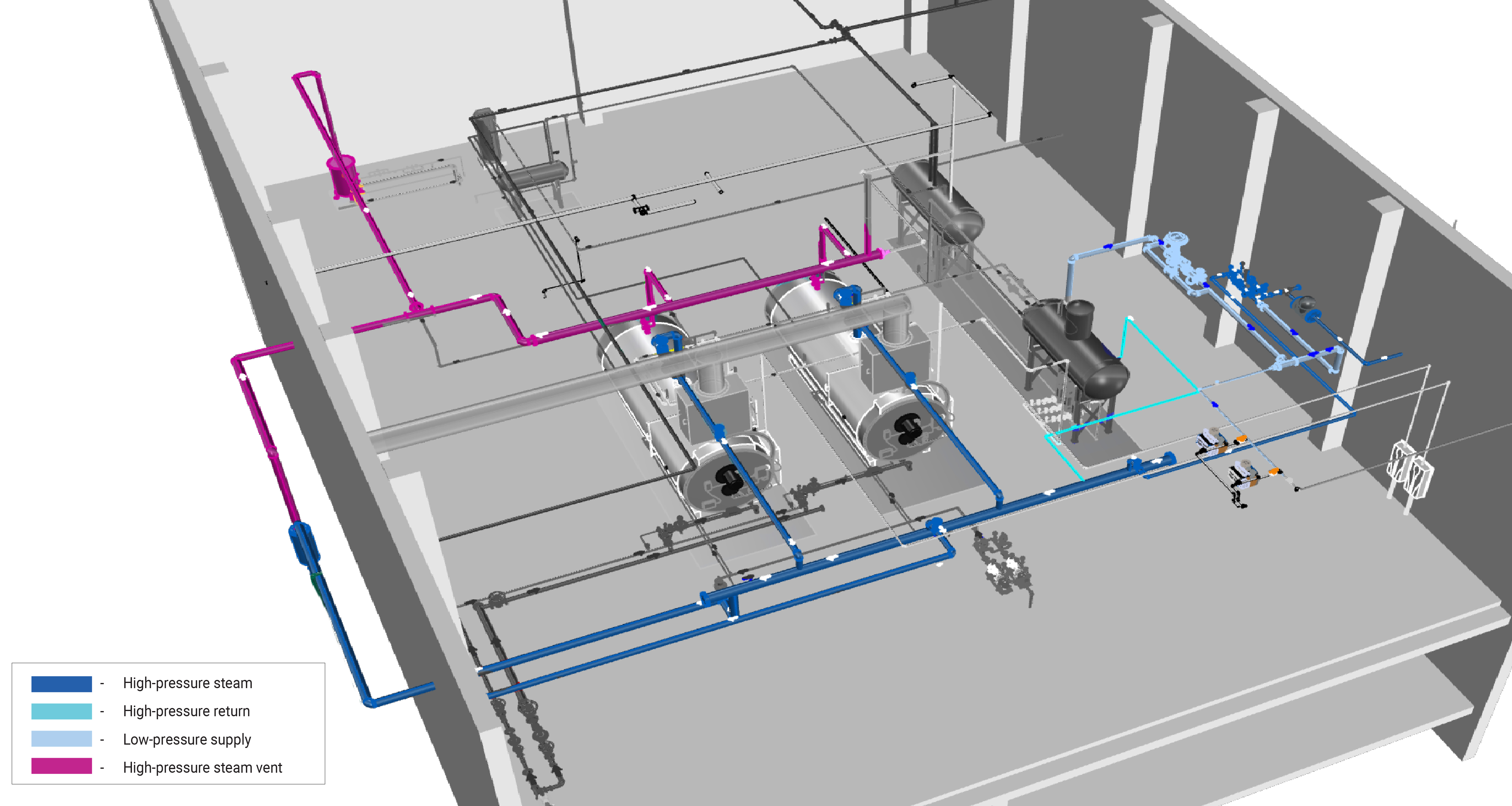
Condensate Recovery System
A condensate recovery system complements the steam distribution system to maintain the efficiency of the steam plant. The condensate usually returns to the boiler, minimizing the feedwater and fuel supply to the boiler. Learn More
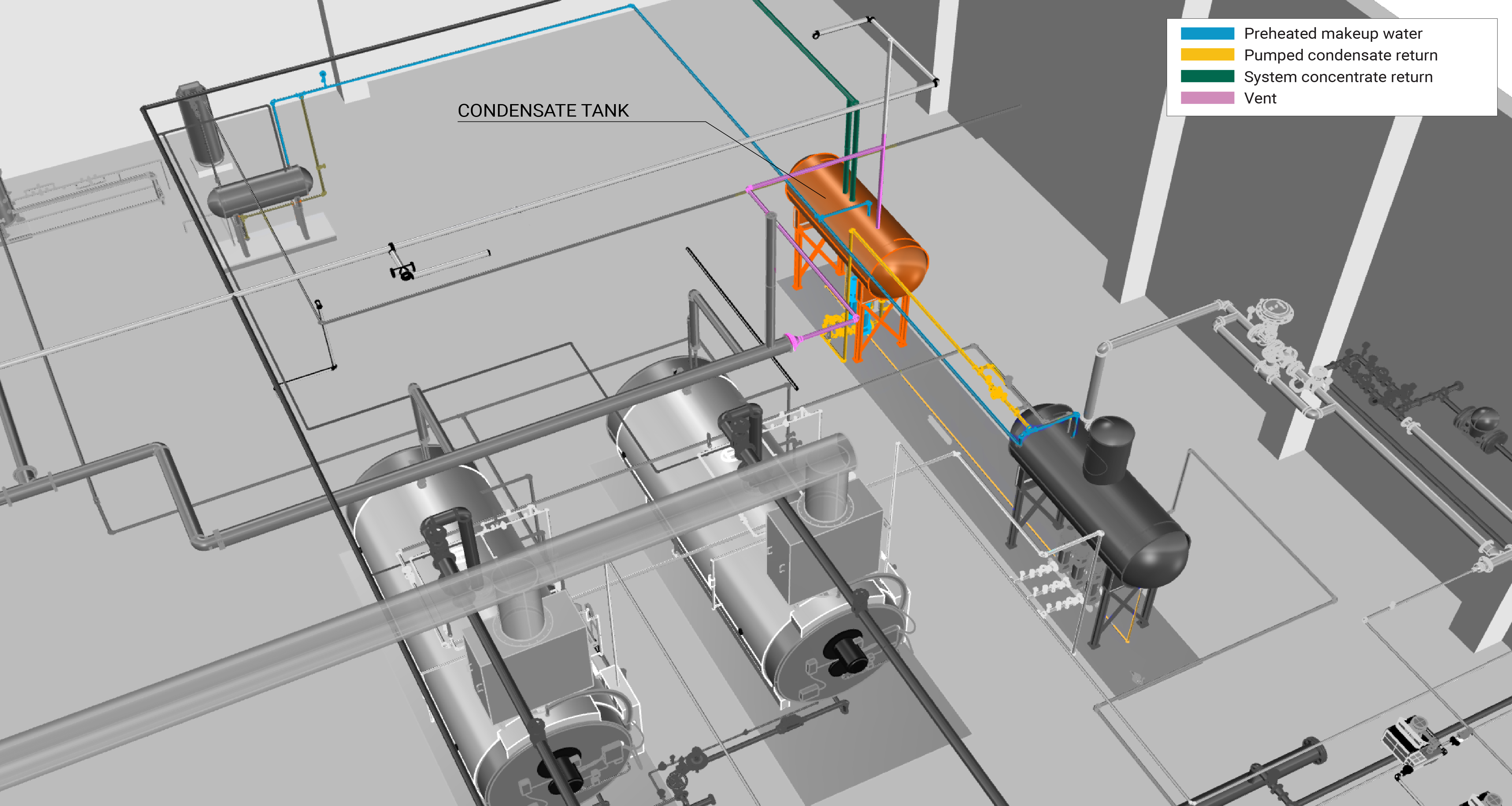
Feedwater System
The feedwater system provides fresh or, at times, treated water to the steam boiler system and allows for removal of water that contains pollutants (i.e., unwanted minerals and/or sediment). This increases the longevity of the system equipment, at a cost of the energy required to heat the feedwater, which is colder than the recirculated condensate. Feedwater systems may include a heat exchanger – commonly called an economizer – which recovers heat from the boiler fuel gases and uses it to pre-heat the feedwater. Learn More
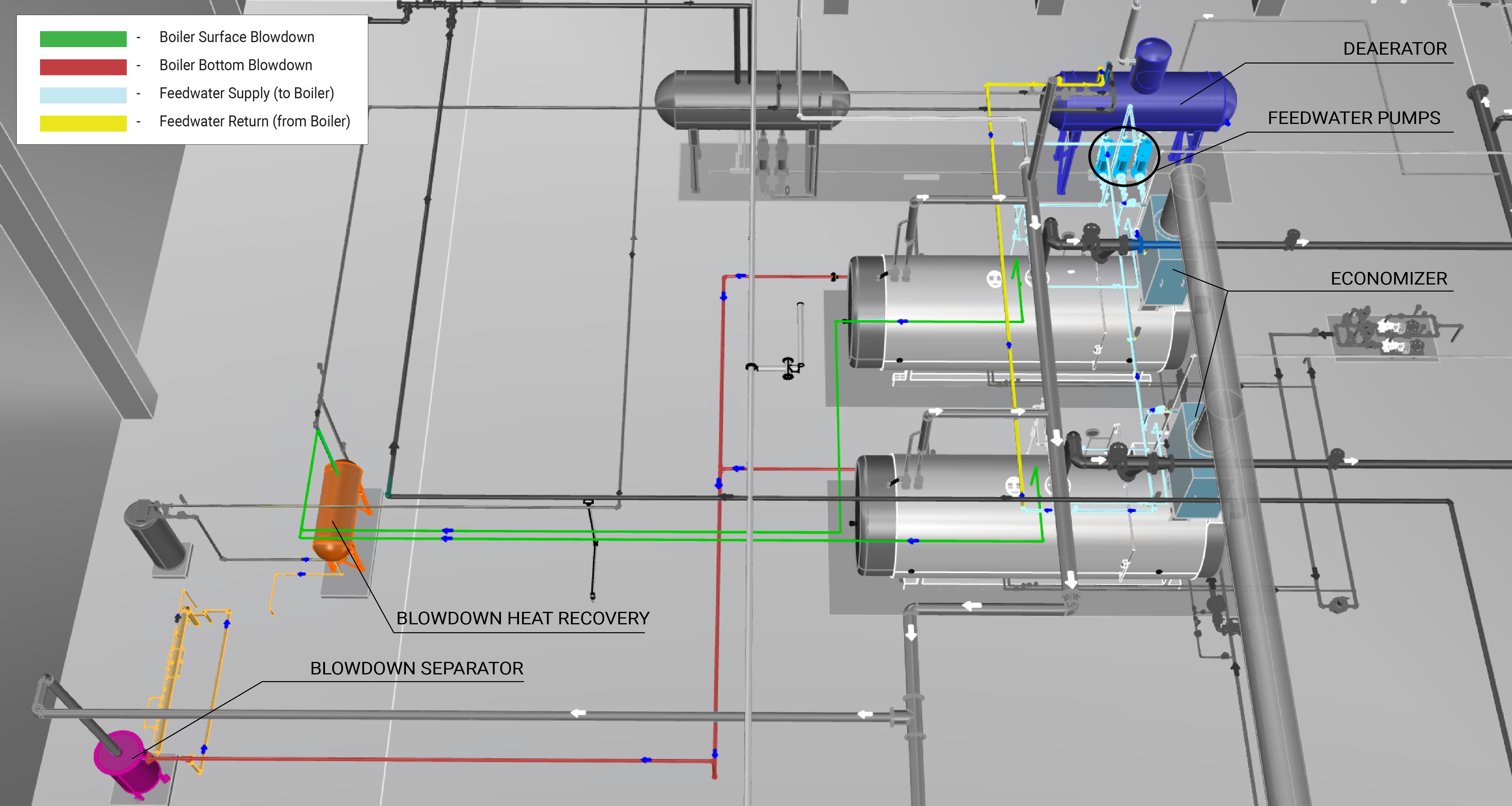
Blowdown System
The blowdown system removes suspended solids and sludge from the boiler water to maintain the operation and efficiency of steam plant components. An integrated blowdown system minimizes unnecessary blowdown by monitoring water quality and allows heat recovery from the blowdown water to preheat feedwater, generate service hot water, or support other applications.
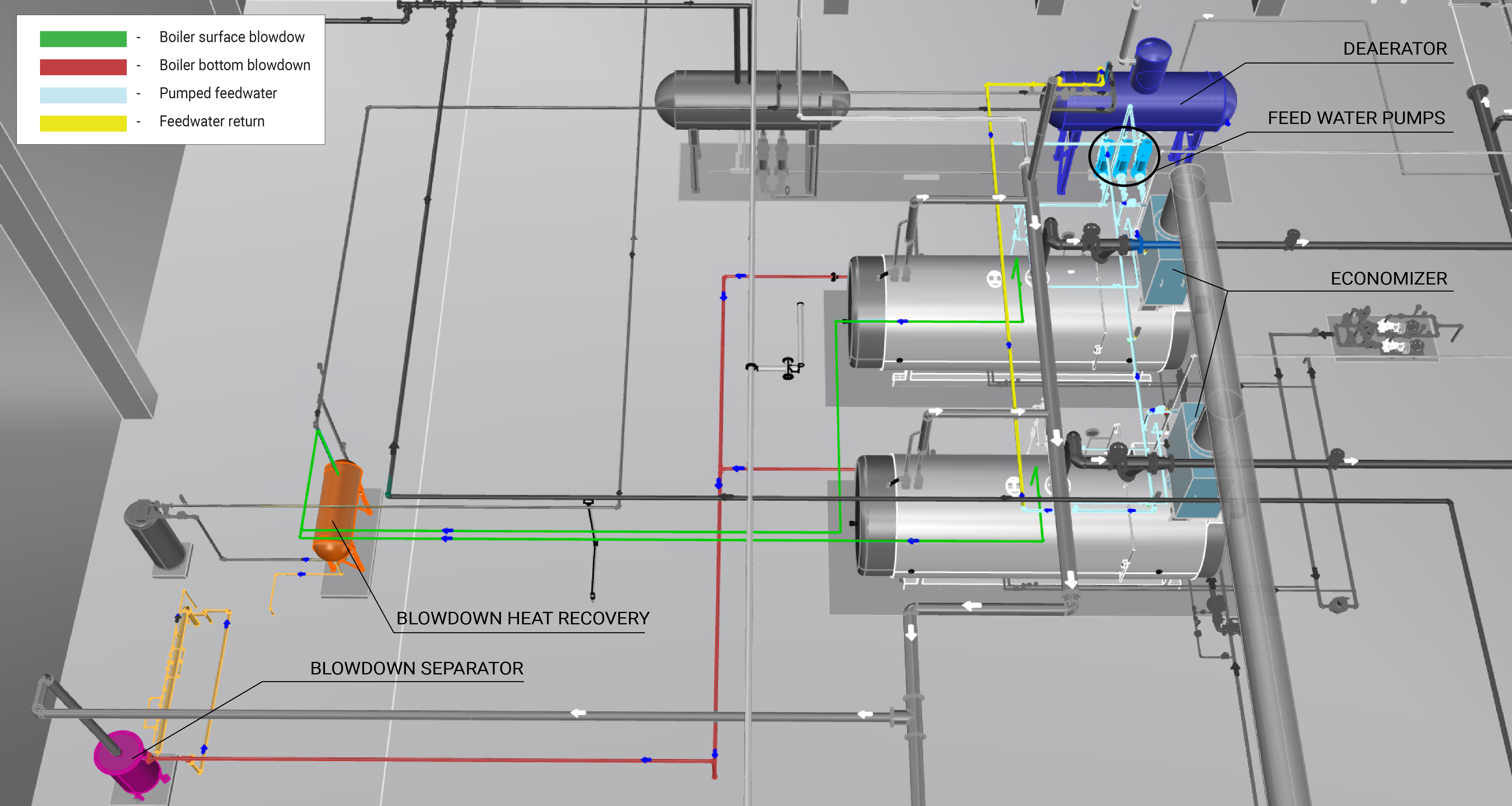
Evaluation of Energy Consumption
The total energy consumption of a steam plant is the sum of the energy used by its individual components. This includes the fuel consumed by the boiler to meet the building’s heating load and the electricity required to operate the burner fan motor, condensate pump, and feedwater pump. Table 1 summarizes the system component measurements and values needed to quantify the annual energy consumption and operating characteristics of the steam plant.
Plant Quantification | Values to be Quantified | Energy Consuming Component |
---|---|---|
Steam boiler plant fuel consumption (Btu) | Average hourly fuel consumption (Btu/h) | Boiler |
Steam plant electricity consumption (kWh) |
|
Further Reading
-
ASHRAE (2020). “ASHRAE Handbook: HVAC Systems and Equipment,” Chapter 11. STEAM SYSTEMS. I-P Edition.
-
ASHRAE (2020). “ASHRAE Handbook: HVAC Systems and Equipment,” Chapter 32. BOILERS. I-P Edition.
-
ASHRAE (2019). “ASHRAE Handbook: HVAC Applications,” Chapter 50, Section 2.5. WATER TREATEMENT: DEPOSITION, CORROSION, AND BIOLOGICAL CONTROL. I-P Edition.
-
Spirax Sarco (2022). “Learn More About Steam” Steam Insights. https://www.spiraxsarco.com/learn-about-steam.